
WORKING PROCESS



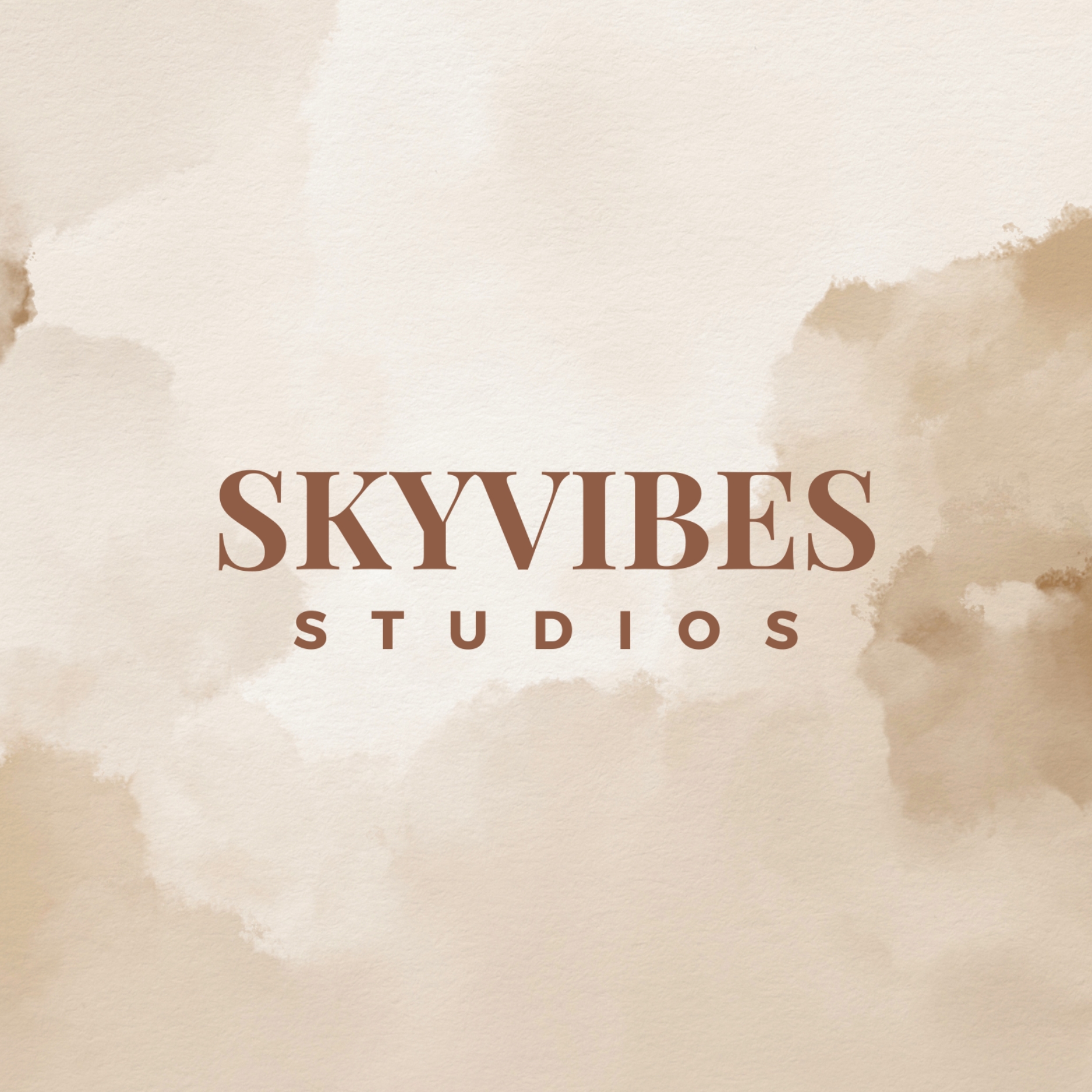
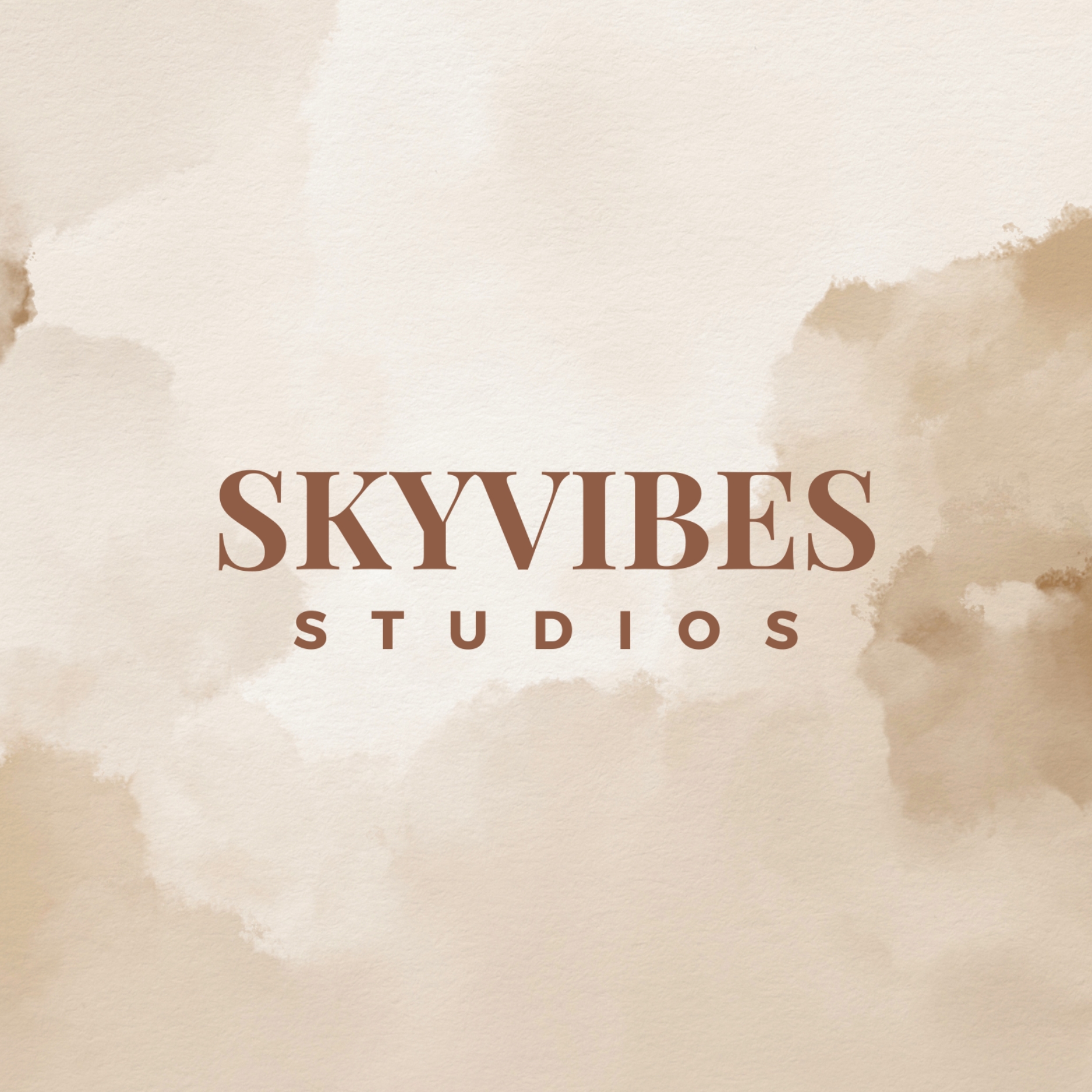
we are dealing in
METHOD OF PRODUCTION
The making process involves different stages such as clay refining, clay mixing, throwing on the wheel, drying and firing.
- Clay Refining and Mixing
In the Initial stage the clay is refined by removing the dust particles like stones, lumps and other impurities in the clay. This is done manually using fine nets to filter the dry clay. Now the raw materials are added with water to prepare the dough. The craftsmen mix the clay by stamping and crushing for the better mixing of clay.
- Throwing Process
The throwing process is done on the potter’s wheel. The mixed clay is placed on the center of the wheel. Then the wheel is rotated. As the wheel starts rotating, the craftsmen start to shape the clay into the required form. Different parts of the object are turned separately and then joined together later. Smoothening of the outer surface is done with wet cloth. This process is repeated until the required thinness is achieved. The object is allowed to dry under the sun for 2 to 3 days. The object is also not dried for a longer period as it becomes very tough. Some products are also covered with clothes to avoid excess drying and cracks on the surface of the object.
- Firing the Clay Objects
The firing is done in the Bhatti-traditional open furnace within a circular area. The articles are piled carefully and covered by locally available fuel such as small wooden pieces etc. The kiln is covered with mud and fired to produce a very high temperature. The objects after firing turn into different colours such as natural, light pink and red because of weather moisture and air. The texture of this product can’t be manually controlled. The red colour is obtained when the smoke comes out through the vents of the kiln. Where in the black colour is obtained by covering the vents completely without allowing the smoke to come out. The objects/ products after firing are tested and segregated by separating the good quality pieces and the damaged ones.
Materials used
The making process involves different stages such as clay refining, clay mixing, throwing on the wheel, drying and firing.
Are they suitable for outdoor use? Are they frost-proof?
Terracotta pots are a great option for indoor and outdoor use. Yes, they are frost-proof as these products are fired at 900-1180 degree Celsius. That’s why these products are strong enough to bear any kind of weather either snow, rainy and hot summers.
Other Information
- It is 100% natural and recyclable.
- It is durable.
- It requires no maintenance.
- It comes in a wide variety of shades.
IMAGES
METHOD OF PRODUCTION
The production process of furniture involves several stages, from material selection to the final finishing touches. Here is a general outline of the method of production for furniture:
- Wood Selection
The primary step in the furniture manufacturing process is the selection of material. Its nature should depend on the piece of furniture you intended to produce with it. For instance, heavy furniture like wooden tables and bedframes require tough, durable materials like hardwoods (mahogany, teak, oak, etc.).
They can endure daily use, support weight, and be waxed and polished to maintain their colour and smooth finish for years. On the other hand, if you want to make decor like kitchen cabinets, supporting beams, window frames and outdoor decks, then softwoods such as fir, ash or birch would do.
- Wood Transformation
This is when the tree is cut into manageable beams and planks, called lumber (North America) or timber (elsewhere). These pieces are the raw material that get sawn and made into wooden furniture. The lumber is kiln-dried, so that the wood achieves its equilibrium moisture content (EMC), and does not gain or lose moisture because of its environment. At the same time, it retains the essential properties of wood. This transformation process is carried out at the sawmill, and its entirety can take about 2 to 4 weeks.
- Wood Splitting & Finishing
The kiln-dried wood is then passed to a machine shop, where it is sawed, planed, moulded and grooved as required. The different parts are cut out and clamped together and then brought in contact with a high-speed rotating knife that shapes each part to its proper size. The pieces are rough-carved on high-speed knives to be machine sanded, and finished by a hand carver later. Veneering, where thin decorative pieces of wood are bonded onto the original surface for a better appearance, is performed at this stage if required. The veneer itself can also be sanded, stained or painted. This is followed by jointing processes like tenoning, doweling and dovetailing.
- Assembly & Quality Check
This is the step where the wooden carcasses (basic frameworks) are assembled, drawers are glued up, and doorframes are put together. Once the glue sets in and clamps are applied, the piece is sent to the machine department for machining that could not be performed before assembly. This includes sanding the joints and shaping the edges. Once this is complete, it is returned to the assembly department for the final structuring, wherein the piece is cleaned to remove excess glue. Hand sanding is done where required, followed by staining, spray polishing and treatments if any.
PROCESS OF PAPER MACHE
The creation process of a paper mache product involves several stages, including refining the paper pulp, mixing it with adhesive, shaping it on a mold, allowing it to dry, and finally, applying a protective coating.
- Method of Production
The raw material used in making of Papier- Mache products is just waste paper of any kind. In this process we soak waste paper in for couple of days in water and then crush into a crusher machine to made pulp. To make Papier-Mache décor products we use moulds of sand casting by the artisan. It is all handmade after creating into a shape The object is allowed to dry under the sun for 2 to 3 days then product has to be get finished and coloured.
No, Paper-Mache products are not for outdoor. It is not water resistant. It is only for indoor and décor. They are not frost-proof.
Materials used
Waste Paper
Are they suitable for outdoor use? Are they frost-proof?
No, Paper-Mache products are not for outdoor. It is not water resistant. It is only for indoor and décor. They are not frost-proof.
Other Information
- It is 100% natural and sustainable.
- It is durable.
- It requires no maintenance.
- It comes in a wide variety of shades.
- Its very light in weight.
- It’s eco-friendly.
- It enhances beauty of homes.